Lead-acid batteries, invented in 1859 by French scientist Gaston Planté, are among the oldest rechargeable battery technologies. Despite the advent of newer battery chemistries, lead-acid batteries continue to play a crucial role in modern energy storage due to their reliability, cost-effectiveness, and ability to deliver high surge currents. They are particularly prominent in automotive, industrial, and backup power applications.
A critical component of these batteries is the lead-acid battery plates. These plates are where the vital chemical reactions take place to store and release electrical energy. By understanding the composition, manufacturing processes, and performance factors of these plates, battery manufacturers can optimize the efficiency and longevity of lead-acid batteries.
Key Components of Lead-Acid Battery Plates
The plates in lead-acid batteries are primarily composed of lead dioxide (PbO₂) for the positive plates and sponge lead (Pb) for the negative plates. These materials are specifically chosen because they facilitate the electrochemical reactions necessary for energy storage. The plates are submerged in an electrolyte solution, typically composed of sulfuric acid (H₂SO₄), which allows ions to migrate between the plates during the charging and discharging processes.
There are two primary types of plates used in lead-acid batteries: flat plates and tubular plates. Flat plates are commonly used in automotive batteries, while tubular plates are more frequently found in deep cycle batteries used for industrial applications, such as solar energy storage and backup power systems. Tubular plates are particularly advantageous in applications that require frequent discharges, as they offer enhanced durability and a longer lifespan.
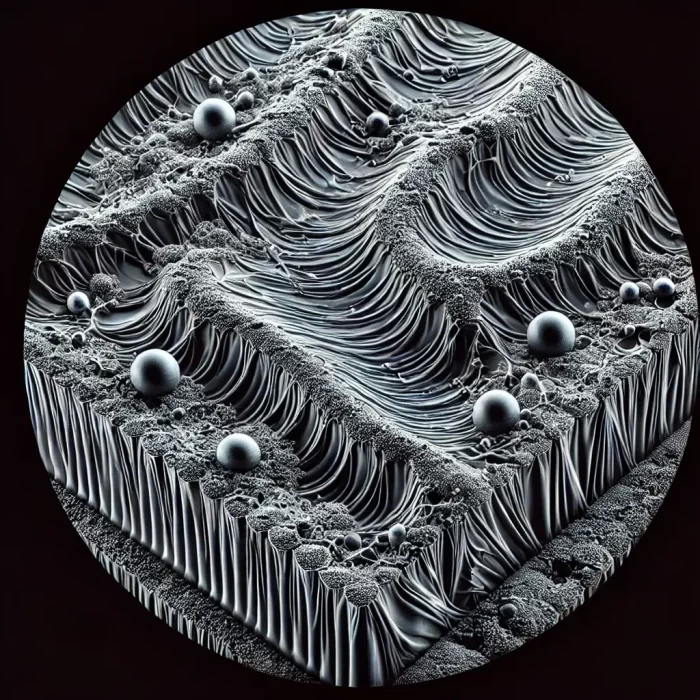
The Manufacturing Process of Lead-Acid Battery Plates
The manufacturing of lead-acid battery plates remains a crucial aspect of battery performance, with recent advancements improving efficiency and sustainability. Key stages in the process are:
- Leady Oxide Production: Leady oxide is still the primary active material for plates, but modern methods emphasize enhanced control over particle size and purity. The two prevalent production methods are the ball mill process and the Barton pot process, both refined over time for better efficiency and environmental impact.
- Ball Mill Process: Lead is ground into a fine powder in a rotating drum, where improvements in automation allow precise control over the lead oxide\’s particle size, surface area, and reactivity. This results in consistent battery performance and longer battery life.
- Barton Pot Process: Lead is melted and atomized into droplets, which oxidize to form leady oxide. Advances in this process have led to better thermal control and less energy consumption, reducing the environmental footprint. Moreover, innovations in particle collection techniques ensure higher purity, benefiting the overall battery performance.
- Sustainability and Safety Enhancements: Recent shifts in the industry focus on reducing lead emissions and improving workplace safety. Closed-loop systems for lead recycling and dust collection are now common, along with stricter compliance with environmental regulations, which has made the production process safer for both workers and the environment.
- Paste Preparation: After the leady oxide is produced, it is mixed with water, sulfuric acid, and other additives to create a paste. This paste is then applied to the battery grids, which serve as the structural framework for the plates. The composition and quality of the paste play a crucial role in determining the amount of active material available for electrochemical reactions within the battery.
During the paste preparation process, it is essential to carefully control the phase composition of the leady oxide. The crystallization of basic lead sulfates in the paste can significantly impact the structure of the active material and, consequently, the battery\’s cycling performance. For example, the balance between the tetragonal and orthorhombic modifications of lead oxide in the paste can influence both the quality and longevity of the battery plates.
- Grid Pasting: The next step in the manufacturing process is pasting the leady oxide paste onto the battery grids. These grids are typically made from a lead alloy and serve two primary functions: providing mechanical support for the paste and conducting electricity between the plates and the external circuit. The quality of the grid paste application is critical for ensuring that the active material remains securely attached to the grid during the battery’s operation.
- Curing: After the paste is applied to the grids, the plates undergo a curing process, which involves the application of controlled temperature and humidity. This step is vital for converting the lead oxide in the paste into basic lead sulfates, which helps to bond the paste firmly to the grid. Proper curing is essential for the structural integrity of the plates, ensuring they can withstand the mechanical stresses of repeated charging and discharging cycles.
- Plate Formation: The final step in the manufacturing process is the formation of the plates. This involves subjecting the plates to several controlled charge and discharge cycles, which convert the lead sulfates into active materials. For positive plates, this material is lead dioxide (PbO₂), while for negative plates, it is sponge lead (Pb). The formation process also creates porosity in the active material, which is crucial for allowing the electrolyte to penetrate the plates and participate in the electrochemical reactions.
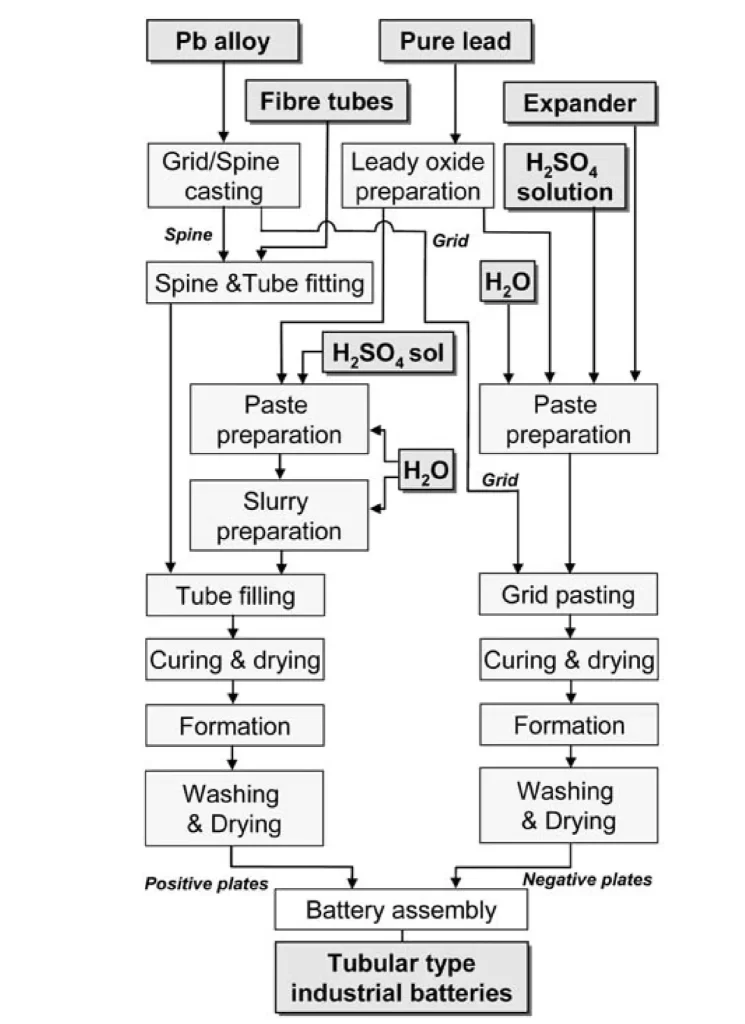
Key Factors Influencing Lead-Acid Battery Plate Performance
The performance of lead-acid battery plates is determined by several critical factors, including the particle size distribution, specific surface area, and phase composition of the leady oxide paste.
- Particle Size Distribution: The particle size of the leady oxide has a significant impact on battery performance. Finer particles provide a larger surface area for electrochemical reactions, resulting in higher initial capacity. However, excessively fine particles can lead to a rapid decline in capacity after repeated cycling. On the other hand, coarser particles offer lower initial capacity but provide a more gradual decline over time, resulting in a longer cycle life. For most applications, medium-grained leady oxide powders with particle sizes ranging from 5 to 50 µm are preferred, as they offer a good balance between high initial capacity and long cycle life.
- Specific Surface Area: The specific surface area of the leady oxide particles is another crucial factor in determining battery performance. A higher specific surface area increases the reactivity of the paste, allowing for faster electrochemical reactions and improved current deliverability. The manufacturing process parameters, such as the temperature in the Barton pot or the milling conditions in the ball mill, can be adjusted to control the specific surface area of the leady oxide and optimize the battery\’s performance.
- Phase Composition: The phase composition of the leady oxide paste plays a critical role in the stability and performance of the active material. For example, the presence of Alpha-PbO in the paste can improve the stability and durability of the active material, leading to better battery performance and a longer service life. Careful control of the phase composition during paste preparation, curing, and formation is essential for producing high-quality battery plates.
Applications and Relevance of Lead-Acid Battery Plates
Lead-acid battery plates are used in a wide range of applications, from automotive starter batteries to industrial-scale energy storage systems. Their ability to deliver high currents and withstand frequent cycling makes them indispensable in many critical applications.
- Automotive Batteries: In automotive applications, lead-acid batteries are used to start the engine and power the vehicle\’s electrical systems. The plates in these batteries must be capable of delivering large surge currents while withstanding frequent charging and discharging cycles. Durability and reliability are key factors in ensuring that the battery provides consistent performance over the life of the vehicle.
- Industrial Batteries: In industrial applications, lead-acid batteries with tubular plates are often used in deep cycle applications, such as renewable energy storage, backup power systems, and electric forklifts. These batteries are designed to withstand deep discharges and a large number of charge/discharge cycles, making them ideal for demanding environments where reliability is critical.
- Backup Power Systems: Lead-acid batteries are also widely used in backup power systems for telecommunications, data centers, and emergency lighting. The ability of lead-acid battery plates to deliver high currents and maintain capacity over extended periods of inactivity makes them well-suited for these applications.
Conclusion: Optimizing Lead-Acid Battery Plate Performance for Enhanced Battery Life
The performance and longevity of lead-acid batteries are heavily influenced by the quality of their plates. By carefully controlling the manufacturing processes, such as leady oxide production, paste preparation, grid pasting, curing, and plate formation, manufacturers can produce high-performance batteries that meet the specific needs of various applications.
Advances in materials science and manufacturing techniques continue to improve the efficiency and reliability of lead-acid batteries. The development of nanostructured materials and other innovations hold the promise of further enhancing the performance of lead-acid battery plates, ensuring that these batteries remain a critical component of modern energy storage solutions for years to come.
In conclusion, lead-acid battery plates are at the heart of this time-tested energy storage technology, and ongoing research and development efforts will continue to optimize their performance for a wide range of applications.